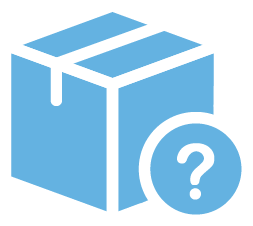
Need help choosing the right product?
Our tool will match the best product to your needs
Launch product selectorWelcome to the United Kingdom Website
We have detected that you may prefer the Global site. Please use the language dropdown above to change your selection if required.
Heat treatment is a Nadcap℠ ‘special process’. Any process that can change or alter a part’s material or physical integrity by introducing stresses via mechanical, thermal, or chemical operations may be considered a special process and must be given particular care to avoid potential defects. AMS2750 was created to provide standardized pyrometry requirements (temperature measurement) in the heat treatment of products for the aerospace industry. Organizations need qualified employees and a well-documented set of procedures and approved equipment to provide evidence that proves both the procedure and results of each batch processed. Nadcap acts as the approval body for ‘special processes’ for aerospace manufacturing and is administered by the Performance Review Institute (PRI). Regular audits are undertaken to ensure facilities meet the requirements. AMS2750 is also referenced in other special process standards and has been adopted in different forms for the automotive (CQI9), oil & gas, and other industries.
Find out how our AMS2750H pyrometry solutions can help you:
The AMS2750 specification covers pyrometry requirements for equipment used in the thermal processing of metallic materials. The following provides an overview of the main sections addressed by Eurotherm products. Please refer to the AMS2750H standards for the full detail (www.sae.org).
Figure 1
Figure 2
Temperature sensors (section 3.1)
This section in the standard outlines the sensor job, use, type, calibration and accuracy requirements. Figure 1 gives an example of common thermocouple types and accuracy requirements.
Thermocouple construction includes both expendable (any portion of the thermal element exposed to the process environment) and non-expendable thermocouples (thermal element protected from the process environment e.g., metal sheath).
Base-metal non-expendable load thermocouple usage is dependent on temperature. Control thermocouple replacement period should be based on data from SAT, TUS, re-calibration, trend analysis and results.
Control thermocouple replacement period should be based on data from SAT, TUS, re-calibration, trend analysis and results.
Figure 3
Instrumentation (section 3.2)
This section outlines the instrument job, type, calibration and accuracy requirements.
Figures 3 and 4 outline the key instrument type requirements supplied by Eurotherm.
Data recording instruments should be checked annually to the accuracy of ±1 min/h by an external timing device (timing device calibrated every 2 years to ±1 s/min).
A possible alternative is to document digital synchronization to NIST (or equivalent) via satellite, internet, or phone (at least monthly) to support these accuracy requirements.
Figure 4
Thermal processing equipment (section 3.3)
This section defines the furnace class (1-6) uniformity tolerance and the instrumentation type (A-E).
SAT (section 3.4) describes a probe check to assess the variation from the process control systems with an independent master thermocouple and field instrument.
TUS (section 3.5) is used to assess the temperature variation within a qualified work zone with respect to setpoint temperature.
Figure 5
Figure 6
When subject to the necessary field calibration, the following instruments manufactured by Eurotherm are suitable for use in the aerospace industry (Nadcap/AMS2750) and automotive (IATF16949/CQI9 version 4).
Process control or recording (AMS2750H Table 7)
Calibration to meet ±2.0°F or ±1.1°C or ±0.2% of temperature, whichever is greater.
Figure 7
6000 series graphical recorder, model numbers: 6100A TUS and 6180A TUS with external CJC and fast-acting accuracy to meet ±1.0°F or ±0.6°C or ±0.1% of temperature, whichever is greater.
¹Devices for use in data acquisition (AMS2750H 3.2.4). Please refer to table below for electronic record solutions. Simple Network Time Protocol (SNTP) is available in the 6000 series graphical recorder, nanodac recorder/controller, E+PLC range, PAC system hardware (model numbers T2550, T2750), and Eycon 10/20 visual supervisors to provide digital synchronization to help meet recording timing accuracy.
Figure 8
Eurotherm control and data recording solutions are IoT ready, providing a data integrity layer within open IoT platform system architectures. Engineered solutions offered by Eurotherm include SCADA, MES, and IIoT system platform technologies for enhanced information visibility, data access and operations management. Our products, systems and services are designed with cybersecury-in-mind, aiding the digital transformation to Industry 4.0 technology.
Product Selector
Our tool will match the best product to your needs
Launch product selectorContact Us