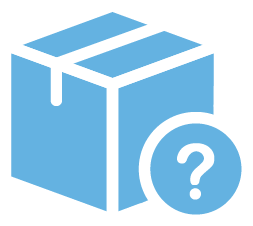
Você precisa de ajuda para escolher o produto certo?
Nossa ferramenta irá combinar o melhor produto para suas necessidades
Iniciar selecionador de produtosBem-vindo ao site da Brazil
Detectamos que você pode preferir o site United Kingdom. Por favor, use o menu de idiomas acima para alterar sua opção se necessário.
This is because there are always some functions that cannot be performed by the normal control system; or there may be unforeseen requirements that need an extra device of some kind.
Look round your process and you might see small hockey-puck shaped components on the heads or inside the covers of temperature sensors. You might find others in a different package around the plant and inside control enclosures, mounted on a bulkhead or on a DIN rail. There is a good chance that these are signal conditioners, doing jobs that complement that of your main control system. These are essential items in the inventor’s tool kit.
They are stand-alone components whose internal circuitry is usually powered by the normal 115V ac line or by a 24V dc supply. They can alternatively be loop powered which means that the power for a device has to come from an incoming or an outgoing 4 – 20mA circuit driven by its own dc power supply.
Signal conditioners have at least one pair of input and one pair of output terminals. The power supply pair can be omitted if you take loop power from a 4 – 20 mA input or output signal. Outside that you can have a rich variety of features that can only be briefly covered in this column. Call or surf your instrumentation supplier for specific details and application examples.
Signal isolators. Here the conditioner may come as a millivolt in and voltage out model, with isolation, adjustable gain and offset, high input impedance and a robust low-impedance output signal.
A current in/current out isolator would also offer adjustable gain and offset. It would have near zero input impedance (current sink) and very high output impedance (current source). Voltage/current and current/voltage isolators are also available. De facto standard process signals are 0-10V dc and 4 – 20mA dc. Five-way isolation applies between input, output, power supply, relay contacts and ground. The isolation is commonly designed to withstand 700V rms ac and 1000V peak. Some models can withstand up to 4000V peak.
Another option is inversion whereby the output increases from 0 – 100% as the input decreases from 100 to 0%. of working range. This could for example, make a reverse acting control loop into direct acting. Gain and offset adjustments are usually provided. This would allow you, for example, to adjust the working range of a control valve. Major benefits of isolation are reliable operation in electrically noisy plants and the elimination of common-mode and ground-loop problems.
Thermocouple to dc mA with isolation. This gives a robust interference-free signal and enables use of copper extension cable in place of the more expensive and higher resistance thermocouple extension cable. Two things to bear in mind. Most low-cost models come with only one choice out of a selection of the most popular thermocouples. This would be factory configured and not field configurable. The output signal would conform to the same non-linear law as the thermocouple. This means that you must take account of the inaccuracy if you use a linear receiving indicator or recorder.
mV, Volt and mA signal scaling. The gain function may be selected to be linear, or to follow a mathematical function or to follow a custom curve. A square root function requirement is common when handling flow signals. A custom curve could be used in two ways. 1. to linearise a grossly non-linear final control element which otherwise would harm control stability. 2. to linearise an uncommon non-linear sensor.
Math functions. Some models have multiple inputs that can be manipulated mathematically to form the output.
The output of V/f converters can be monitored over great distances over a telephone line then
easily reconverted to represent a process measurement at the receiving end using an f/V converter.
Models are available with multiple and mixed inputs and outputs.
In one case a Btu/h measurement was required, calculated from mass flow rate x (T2 – T1).
Inlet and outlet temperatures T1and T2 were taken from two RTDs into a three-input conditioner. The third input was a frequency signal representing flow from a mass flowmeter.
The temperature difference T2 – T1 was obtained then multiplied by the frequency signal. The resulting dc output was scaled to show Btu/h. A second conditioner took in the dc Btu/h signal and converted it to a frequency where each cycle represented a fixed number of Btus. The frequency was suitably scaled and totalised as Btus on an electric counter.
Later versions of conditioner can derive the same two results using only one conditioner with multiple inputs and outputs.
3-terminal Potentiometer to high-level dc.
Two applications here: Retransmission to control room of gate position on a hydro-electric station. Manual adjustment of a remote electro-pneumatic damper positioner.
Potentiometer to pulse-width modulation.
One application example is manual adjustment of percentage input of a heat process. The heat source could be gas, electricity or a heat transfer medium.
Strain gage output to high level dc.
Weight measurement and batch loading applications.
Alternating voltage and current inputs.
AC inputs can be converted to signals representing voltage, current, power, reactive power,
kVA, power factor and, with a frequency output, pulses representing watt hours per count. Monitoring and alarm annunciation functions can minimise the demand component of energy costs.
Signal input/output configuration.
An increasing number of models now are field configurable in respect of magnitude and type of input and output signal. This can be done by manual adjustments and DIP switches, alternatively by a PC. The upmarket models linearise thermocouple and RTD signals. An LCD display is available on some models to show the process signal or as an aid to field configuration.
Rate of change of signal limiter.
Let’s say your process cannot tolerate more than a certain rate of change of say power input, pressure, flow etc. Some converters offer an adjustable output ramp rate limit in the face of a wildly varying signal input.
Alarm Choices.
Multiple alarm relays or open collector outputs can be specified and configured as high, low, deviation or rate of change of signal.
Communications.
Models are available with RS-232 or RS485 communication capability, providing internet access to process signals and alarm conditions. Remote ranging and some configuration items are also possible.
Intrinsic Safety in this context refers to instruments and low voltage circuits designed to prevent release of sufficient energy to ignite volatile gases. Signal conditioners are available that comply with the rules of intrinsic safety in specified hazardous atmospheres.
Adapted from an article originally written by Arthur Holland, Holland Technical Skills, for Eurotherm.
Selecionador de produtos
Nossa ferramenta irá combinar o melhor produto para suas necessidades
Iniciar selecionador de produtosContete-Nos